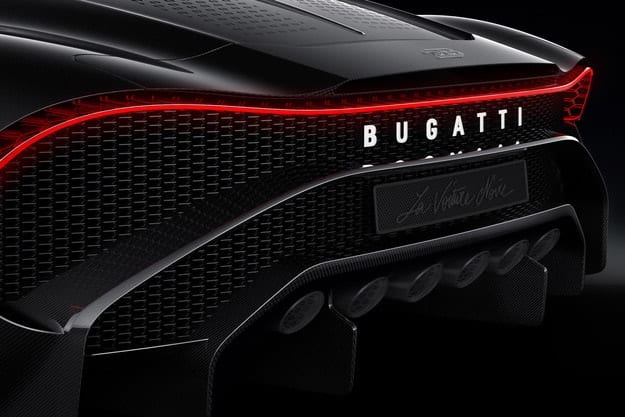
Bugatti: impressió 3D al cor del Quiró
El fabricant francès utilitza aquesta tecnologia el 2018 per al model Chiron Sport.
Des del 2018, el fabricant amb seu a Molsheim utilitza la tecnologia d’impressió 3D per fabricar certes peces d’hipersport Chiron, com ara les puntes d’escapament de titani dels models Pur Sport i Super Sport 300+.
Igual que Ettore Bugatti, fundador de la marca tricolor que presenta periòdicament innovacions en el disseny dels seus models (li devem principalment les rodes d’aliatge i l’eix davanter buit), els enginyers responsables del desenvolupament de nous models Bugatti inclouen les darreres innovacions. en construcció o enginyeria en les seves creacions. Una d’elles és la tecnologia d’impressió 3D, els avantatges dels quals ja són ben coneguts.
Bugatti va utilitzar aquesta tecnologia el 2018 al Chiron Sport, que es va equipar amb puntes d’escapament fabricades en Inconel 718, un aliatge de níquel-crom dur i lleuger especialment resistent a la calor (en aquest cas, l’alumini es fon). Els propers models de la marca (Divo, La Voiture Noire, Centodieci ...) també es beneficiaran d’aquest procés de producció de les seves canonades de sortida.
Aquests elements impresos en 3D tenen diversos avantatges. D’una banda, són més resistents a la calor i eliminen l’acumulació de calor creada pel motor W8,0 de 16 CV de 1500 litres, i també són més lleugeres que els injectors convencionals. (El Chiron Sport pesa només 2,2 kg, per exemple 800 g menys que un injector convencional).
En el cas del nou Chiron Pur Sport, Bugatti fabrica broquets d’escapament de titani impresos en 3D i el fabricant indica que es tracta de “la primera part de metall visible impresa en 3D amb homologació del trànsit rodat”. Aquest accessori té 22 cm de llarg i 48 cm d’amplada i només pesa 1,85 kg (inclosa la graella i el manteniment), aproximadament 1,2 kg menys que el Chiron “estàndard”.
Un sistema d’impressió làser especial que s’utilitza per a la impressió 3D consisteix en un o més làsers que, al seu torn, fonen capes de pols d’entre 3 i 4 micres. 4200 capes de pols metàl·lica s’apilen les unes sobre les altres i es fusionen formant el broquet d’escapament Chiron Pur Sport que suportarà temperatures superiors a 650 graus centígrads, alhora que proporciona aïllament tèrmic a les parts adjacents gràcies a la doble paret exterior.
Aquests elements finalment es revestiran especialment abans de ser inspeccionats i instal·lats acuradament al vehicle. Per exemple, el Chiron Sport està polit amb corindó i lacat en negre amb pintura ceràmica a alta temperatura, mentre que el Chiron Pur Sport i el Super Sport 300+ estan disponibles en un acabat de titani mat.
En garantir la durabilitat, la ultralleugeresa i l’estètica de les peces, la tecnologia d’impressió 3D, fins ara utilitzada principalment en l’aeronàutica i l’espai, sembla que finalment ha trobat el seu lloc entre els fabricants de cotxes, fins i tot els més exigents.
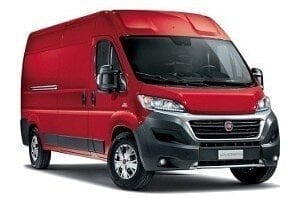
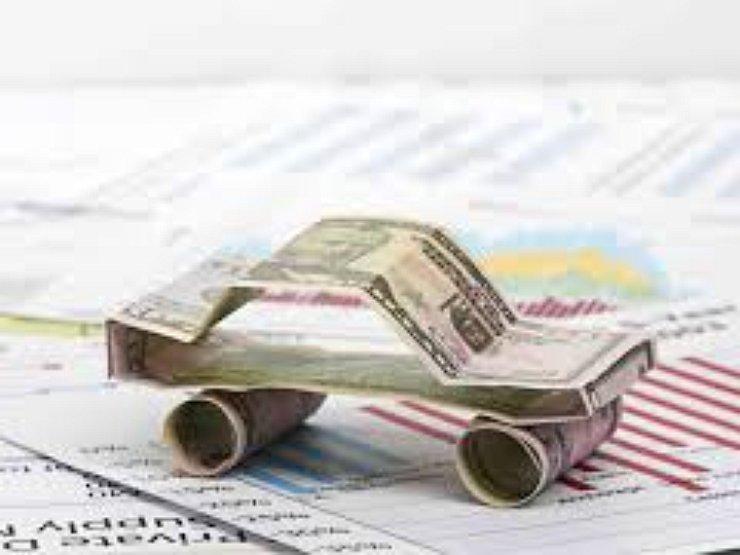