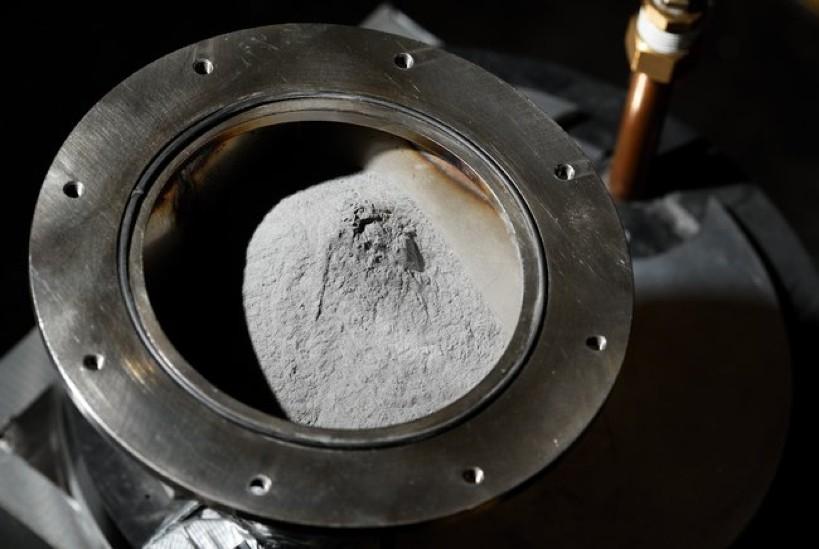
Futur en pols
Contingut
L'empresa sueca VBN Components produeix productes d'acer mitjançant tecnologies d'additius utilitzant pols amb additius, principalment eines com ara trepans i freses. La tecnologia d'impressió 3D elimina la necessitat de forjar i mecanitzar, redueix el consum de matèries primeres i ofereix als usuaris finals una selecció més àmplia de materials d'alta qualitat.
L'oferta de components VBN inclou per exemple. Vibenita 290que, segons l'empresa sueca, és l'acer més dur del món (72 HRC). El procés de creació de Vibenite 290 és augmentar gradualment la duresa dels materials fins a. Un cop s'imprimeixen les peces desitjades a partir d'aquesta matèria primera, no es requereix cap altre processament que no sigui la mòlta o la electroerosió. No cal tallar, fresar ni perforar. Així, l'empresa crea peces amb dimensions de fins a 200 x 200 x 380 mm, la geometria de les quals no es pot produir amb altres tecnologies de fabricació.
L'acer no sempre és necessari. Un equip d'investigació de HRL Laboratories ha desenvolupat una solució d'impressió 3D. aliatges d'alumini amb gran força. Es diu mètode nanofuncional. En poques paraules, la nova tècnica consisteix a aplicar pols nanofuncionals especials a una impressora 3D, que després es "sinteritzen" amb un làser en capes fines, la qual cosa condueix al creixement d'un objecte tridimensional. Durant la fusió i la solidificació, les estructures resultants no es destrueixen i conserven tota la seva força a causa de les nanopartícules que actuen com a centres de nucleació per a la microestructura prevista de l'aliatge.
Els aliatges d'alta resistència com l'alumini s'utilitzen àmpliament en la indústria pesant, la tecnologia de l'aviació (per exemple, el fuselatge) i les peces d'automòbil. La nova tecnologia de nanofuncionalització els proporciona no només una gran resistència, sinó també una varietat de formes i mides.
Suma en lloc de resta
En els mètodes tradicionals de treball del metall, el material de rebuig s'elimina per mecanitzat. El procés d'additiu funciona a la inversa: consisteix a aplicar i afegir capes successives d'una petita quantitat de material, creant peces XNUMXD de gairebé qualsevol forma a partir d'un model digital.
Tot i que aquesta tècnica ja s'utilitza àmpliament tant per al prototipatge com per al modelatge, el seu ús directament en la producció de béns o aparells destinats al mercat ha estat difícil a causa de la baixa eficiència i les propietats del material insatisfactories. No obstant això, aquesta situació està canviant gradualment gràcies al treball dels investigadors de molts centres d'arreu del món.
Mitjançant una minuciosa experimentació, s'han millorat les dues tecnologies principals d'impressió XNUMXD: deposició làser de metall (LMD) i fusió per làser selectiva (ULM). La tecnologia làser permet crear detalls precisos i obtenir una bona qualitat de superfície, cosa que no és possible amb la impressió de feix d'electrons 50D (EBM). En SLM, la punta del raig làser es dirigeix a la pols del material, soldant-lo localment segons un patró determinat amb una precisió de 250 a 3 micres. Al seu torn, LMD utilitza un làser per processar la pols per crear estructures XNUMXD autosuficients.
Aquests mètodes han demostrat ser molt prometedors per crear peces d'avions. i, en particular, la deposició làser de metall amplia les possibilitats de disseny dels components aeroespacials. Es poden fer a partir de materials amb estructures internes complexes i amb gradients que en el passat no era possible. A més, ambdues tecnologies làser permeten crear productes de geometria complexa i obtenir una funcionalitat ampliada de productes a partir d'una àmplia gamma d'aliatges.
El setembre passat, Airbus va anunciar que havia equipat el seu A350 XWB de producció amb impressió additiva. suport de titani, fabricat per Arconic. Aquest no és el final, perquè el contracte d'Arconic amb Airbus preveu la impressió 3D a partir de pols de titani-níquel. parts del cos i sistema de propulsió. Tanmateix, cal tenir en compte que Arconic no utilitza tecnologia làser, sinó la seva pròpia versió millorada de l'arc electrònic EBM.
És probable que una de les fites en el desenvolupament de tecnologies additives en el treball del metall sigui el primer prototip presentat a la seu del grup holandès Damen Shipyards Group a la tardor del 2017. hèlix de vaixell aliatge metàl·lic que porta el nom VAAMpeller. Després de les proves adequades, la majoria de les quals ja s'han fet, el model té la possibilitat de ser aprovat per al seu ús a bord dels vaixells.
Com que el futur de la tecnologia metal·lúrgica rau en pols d'acer inoxidable o components d'aliatge, val la pena conèixer els principals actors d'aquest mercat. Segons l'"Informe del mercat de pols metàl·liques de fabricació additiva" publicat el novembre de 2017, els fabricants més importants de pols metàl·liques d'impressió 3D són: GKN, Hitachi Chemical, Rio Tinto, ATI Powder Metals, Praxair, Arconic, Sandvik AB, Renishaw, Höganäs AB. , Metaldyne Performance Group, BÖHLER Edelstahl, Carpenter Technology Corporation, Aubert & Duval.
Impressió d'hèlix WAAMpeller
Fase líquida
Les tecnologies d'additius metàl·lics més conegudes actualment es basen en l'ús de pols (és així com es crea l'esmentada vibenita) "sinteritzats" i fusionats per làser a les altes temperatures necessàries per al material de partida. No obstant això, estan sorgint nous conceptes. Investigadors del Laboratori d'Enginyeria Criobiomèdica de l'Acadèmia Xinesa de Ciències de Pequín han desenvolupat un mètode Impressió 3D amb "tinta", format per un aliatge metàl·lic amb un punt de fusió lleugerament superior a la temperatura ambient. En un estudi publicat a la revista Science China Technological Sciences, els investigadors Liu Jing i Wang Lei demostren una tècnica per a la impressió en fase líquida d'aliatges a base de gal·li, bismut o indi amb l'addició de nanopartícules.
En comparació amb els mètodes tradicionals de prototipatge metàl·lic, la impressió 3D en fase líquida té diversos avantatges importants. En primer lloc, es pot aconseguir una taxa relativament alta de fabricació d'estructures tridimensionals. A més, aquí podeu ajustar de manera més flexible la temperatura i el cabal del refrigerant. A més, el metall conductor líquid es pot utilitzar en combinació amb materials no metàl·lics (com els plàstics), cosa que amplia les possibilitats de disseny de components complexos.
Els científics de l'American Northwestern University també han desenvolupat una nova tècnica d'impressió 3D metàl·lica que és més barata i menys complexa que la que es coneixia anteriorment. En lloc de pols metàl·lica, làsers o feixos d'electrons, s'utilitza forn convencional i material líquid. A més, el mètode funciona bé per a una gran varietat de metalls, aliatges, compostos i òxids. Això és similar al segell de broquet que coneixem amb els plàstics. La "tinta" consisteix en una pols metàl·lica dissolta en una substància especial amb l'addició d'un elastòmer. En el moment de l'aplicació, es troba a temperatura ambient. Després d'això, la capa de material aplicada des del broquet es sinteritza amb les capes anteriors a una temperatura elevada creada al forn. La tècnica es descriu a la revista especialitzada Advanced Functional Materials.
Mètode d'impressió en fase de metall líquid xinès
El 2016, els investigadors de Harvard van introduir un altre mètode que pot crear estructures metàl·liques en XNUMXD. imprès "a l'aire". La Universitat de Harvard ha creat una impressora 3D que, a diferència d'altres, no crea objectes capa per capa, sinó que crea estructures complexes "a l'aire", a partir de metall que es congela instantàniament. El dispositiu, desenvolupat a l'Escola d'Enginyeria i Ciències Aplicades John A. Paulson, imprimeix objectes amb nanopartícules de plata. El làser enfocat escalfa el material i el fusiona, creant diverses estructures com una hèlix.
La demanda del mercat de productes de consum impresos en 3D d'alta precisió, com ara implants mèdics i peces de motor d'avions, està creixent ràpidament. I com que les dades dels productes es poden compartir amb altres, les empreses de tot el món, si tenen accés a la pols metàl·lica i la impressora 3D adequada, poden treballar per reduir els costos de logística i d'inventari. Com és sabut, les tecnologies descrites faciliten molt la fabricació de peces metàl·liques de geometria complexa, per davant de les tecnologies de producció tradicionals. És probable que el desenvolupament d'aplicacions especialitzades condueixi a preus més baixos i també a l'obertura a l'ús de la impressió 3D en aplicacions convencionals.
L'acer suec més dur per a la impressió 3D:
L'acer més dur del món - fabricat a Uppsala, Suècia
Pel·lícula d'alumini per a la impressió:
Avanç en la metal·lúrgia: impressió 3D d'alumini d'alta resistència

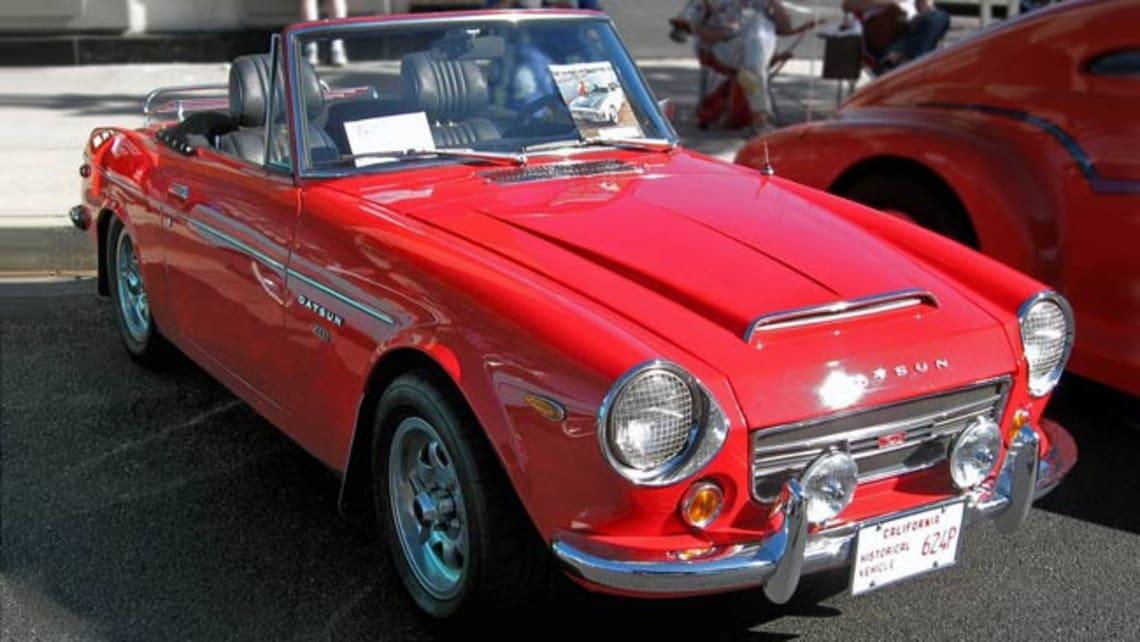
Un comentari
Anònim
divertida